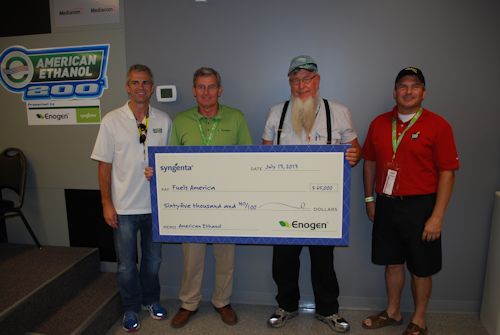
In more ways than one, ethanol was the winner in The American Ethanol 200, a truck race at the Iowa Speedway at Newton on July 13. Prior to the NASCAR race, Syngenta officials held a press conference at the track to make an important announcement involving the seed company's new Enogen corn. They announced that the firm will contribute $1 to the renewable fuels industry for every acre planted with the new Enogen trait technology, beginning with this year's growing season. "We will do this for three years," says David Witherspoon, head of renewable fuels for Syngenta.

BIG CHECK: At a press conference at the Iowa Speedway, Syngenta officials presented a check for $65,000 to Fuels America to help support the Renewable Fuel Standard and to promote ethanol. From left are Kelly Manning, Growth Energy; David Witherspoon, Syngenta; Ray Defenbaugh, Big River Resources (representing Fuels America); and Delayne Johnson, Quad County Corn Processors.
This effort will help support the Renewable Fuel Standard and promote the benefits of renewable fuels grown in America. Witherspoon also provided an update on information about Enogen corn, which has been developed by Syngenta and is being introduced in the marketplace specifically for ethanol production.
Farmers who have a contract with an ethanol plant participating in the Syngenta program can get paid a premium of around 40 cents a bushel for growing Enogen corn. This year Syngenta has contracted with 268 farmers in Iowa, Nebraska, South Dakota and Kansas to grow Enogen corn on 65,000 acres, up from 25,000 acres last year. Syngenta hopes to triple its sales of Enogen seed next year to 175,000 acres--and go way beyond that in the years ahead.
Enogen corn was developed with a trait specifically for ethanol production
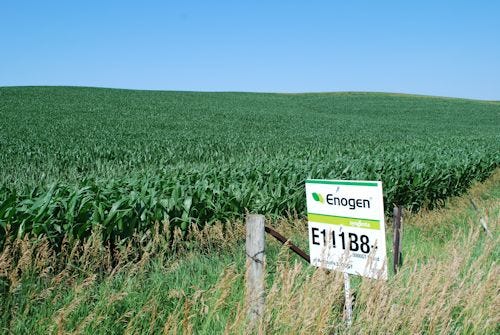
PRICE PREMIUM: Not only do ethanol plants realize various benefits from using Enogen corn, farmers who grow it also reap rewards. Ethanol plants participating in this program contract directly with local farmers to produce and deliver the value-added grain which contains the alpha amylase enzyme. The ethanol plants are paying farmers an average premium of 40 cents per bushel for the identity preserved corn. For some growers, that's an extra $80 to $90 an acre.
Enogen corn kernels contain a significantly higher amount of alpha amylase enzyme than regular corn. "Enogen produces its own alpha amylase, a necessary ingredient for ethanol production," explains Witherspoon. "Farmers can grow Enogen corn on contract and get paid the price premium when they deliver the corn to an ethanol plant that's in the Syngenta program."
Ethanol plants buy the alpha amylase enzyme in liquid form and add it to the corn mash during the ethanol production process. However, by using Enogen corn, ethanol plants can save money because they don't have to buy the enzyme. With Enogen, it comes in the corn. Enogen corn can save ethanol plants money in other ways too, he notes. For example, the mash made from a mix of 90% regular corn and 10% Enogen corn is thinner, it flows easier--resulting in less water, electricity and natural gas used to pump the mash through the ethanol manufacturing process at the plant.~~~PAGE_BREAK_HERE~~~
Only 10% to 20% of an ethanol plant's total corn input needs to be Enogen corn to produce the desired results. Thus, in an area of 40 miles or so around a participating ethanol plant only a certain number of farmers would be needed to grow Enogen corn. For a 50-million-gallon per year plant, for example, the plant would never need more than 25,000 acres of Enogen or roughly 25 to 30 growers contracting to produce this identity preserved corn. What's Syngenta's goal for Enogen acreage in the U.S.? Company officials aren't saying. But they do say Syngenta is targeting all dry mill ethanol plants in the U.S.—about 80% of the nation's 211 ethanol plants.
Syngenta pledges further support for renewable fuels and the RFS
Syngenta's three-year commitment to contribute $1 to the renewable fuels industry for every acre planted to Enogen corn will be used to help fund efforts to support the Renewable Fuels Standard and to promote the benefits of renewable fuels, says Witherspoon. The RFS is under fire in Washington, D.C. these days as the petroleum industry wants Congress to kill the RFS—a law which requires fuel refiners nationwide to blend a certain amount of ethanol in their gasoline each year.
"Renewable fuels are an essential part of the American Energy equation, benefitting consumers, farmers and American energy independence," says Witherspoon. "Ethanol, whether it's made from corn or biomass, is an energy source for today and tomorrow and it is driving economic growth and innovation."
This year the $1 per acre donation by Syngenta is going to an organization called Fuels America, a broad coalition of stakeholders committed to protecting America's Renewable Fuel Standard and promoting the benefits of all types of renewable fuels. "Agriculture has benefitted significantly from the RFS and ethanol," Witherspoon told Wallaces Farmer in an interview after the press conference at Iowa Speedway. "Ethanol has increased the demand for corn, improved prices for farmers and is helping rural America grow in many ways by creating and supporting jobs in the ethanol industry. Syngenta is a company that has been supporting ethanol all along but we're bolstering our effort even more now."
First check is for $65,000 and is presented as a contribution to help the organization "Fuels America" promote and garner support for ethanol
The Enogen dollar-per-acre contribution which starts this year was presented as an "oversize" check for display purposes by Witherspoon at the press conference. The check was for $65,000 made out to Fuels America. Syngenta has 65,000 acres of Enogen corn under contract in 2013 as the program is in its second year of getting started with grower contracts. The goal is to expand Enogen corn acreage in years to come as more ethanol plants participate and offer the price premium to farmers for growing this corn.~~~PAGE_BREAK_HERE~~~
The Enogen corn contracting program started as a pilot program with an ethanol plant near Holstein in northwest Iowa—Quad County Corn Processors at Galva. Last year was the first year Quad County had growers producing Enogen under contract. "The crop being grown in 2013 is our second crop," says Delayne Johnson, general manager of Quad County Corn Processors. "We're now getting ready to contract for our third crop of Enogen corn, which will be grown in 2014."
Growers earn premiums for producing this identity preserved corn, and ethanol plants lower their cost of producing ethanol
Quad County Corn Processors in 2013 has contracts in place with 27 farmers to produce Enogen corn, paying an average premium of 40 cents per bushel. Last year was the first year and with drought conditions it was difficult to make yield comparisons. "But the feedback we've been getting is Enogen corn is yielding the same or very close to the same as other commercial corn hybrids," says Johnson. He notes that 90% of the farmers who grew Enogen corn last year contracted to grow it again this year.
Enogen corn has allowed the ethanol producers who are participating in the program to increase the amount of starch they put in the fermentation tank and use less water in the distillation process. He says the Quad County Corn Processors facility's natural gas usage is about 5% less per gallon of ethanol produced.
"We're always looking for ways to become more efficient and improve our productivity in the ethanol industry," notes Johnson, "so any technology that can help save us money while also increasing our output of ethanol interests us. The idea of creating added value for our local farmers is an additional bonus. Thanks to the Enogen corn we don't have to buy the alpha amylase enzyme and add it to our production process. Along with other savings generated by using Enogen corn in our plant that means we can pay the price premium to our growers and help keep nearly $500,000 per year in our local community. It's a definite financial benefit for us to not have to buy alpha amylase enzyme and add it separately to our processing plant to make ethanol."
For more information visit the Enogen website.
About the Author(s)
You May Also Like